"Christmas gift suggestions: To your enemy, forgiveness. To an opponent, tolerance. To a friend, your heart. To a customer, service. To all, charity. To every child, a good example. To yourself, respect." — Oren Arnold
A blog intended to educate and inform those interested in industrial control instrumentation and process control equipment. Weekly posts on various subjects ranging from pressure / temperature / level and flow instruments, control valves, analytical instruments, drives and actuators, recorders, and process weighing.
For more information, visit the Power Specialties website or call (816) 353-6550
Combustion Air Flow Monitoring: Better Combustion Control Saves Money

Most combustion systems have mechanical controls set to overfeed combustion air by as much as 20%. Fuel costs and additional maintenance costs associated with blower or burner wear can add up to thousands of dollars wasted per day. However, there is a low cost remedy that can be implemented during a short downtime — upgrading combustion air flow meters or installing an instrumented control system.
Benefits of Combustion Airflow Monitoring
- Fuel cost savings
- Improve process stability
- Reduce operator interventions
- Increase equipment capacity
- Improve safety
- Reduce carbon footprint
- Improve sustainability
THE CHALLENGES
How can large combustion processes be modified so they operate more efficiently over a wide
operating range with dirty gases that tend to plug and coat?
- Dealing With Limited Straight Runs
- Tighter Control in High Turndown Situations
- Reducing Plugging and Coating
- Improving Efficiency and Environmental Compliance
![]() |
Air Monitor Corporation Products |
based
Recorded Webinar: Detection Technologies for Toxic and Combustible Gases
This recorded webinar, presented by MSA, provides an excellent overview of the history of gas detection and the technologies used today. MSA is the world's leading manufacturer of safety products designed to protect people throughout the world.
Industrial gas detectors are used in a wide variety of chemical plants, refineries, water treatment plants, and other manufacturing facilities to continuously monitor and detect toxic or combustible gases and vapors. They are equipped with audible and visual alarms to alert personnel to the existence of these conditions. The major components for industrial gas detectors are the sensor, the detector, the transmitter, and the annunciator. Gas detection systems are available as single point sensing or multiple point sensing capabilities, and in fixed position or portable configurations.
For more information about MSA gas detection products, contact Power Specialties. Call them at (816) 353-6550 or visit them at https://powerspecialties.com.
Celebrating Our Veterans on Veterans Day
Veterans Day is a day of observance and celebration for those who have served in the United States military. Veterans Day was originally called Armistice Day because of the November 11 Armistice that ended World War I. In 1954 it was officially changed to Veterans Day to include Veterans of all wars. This holiday honors those who took an oath to defend the United States and our Constitution, from all enemies, foreign and domestic. Through the observance of Veterans Day, we remind ourselves of our Veterans patriotism, love of country and willingness to serve and sacrifice for the common good.
Power Specialties thanks our Veterans, past and present, for serving our country and protecting our freedom.
Electric and Pneumatic Damper Drives for Combustion Air and Flue Gas
![]() |
Download the Damper Drive Catalog Here |
Current combustion control systems lack continuous carbon monoxide and nitrogen oxide emissions monitoring capability and the automated controls needed to improve fuel performance. A novel combustion control system, along with gas sensors, sets the opening of fuel and air inlets based on flue-gas concentrations. Continuous feedback from measurements of oxygen, carbon monoxide, and nitrogen oxide concentrations enable the control system to improve combustion efficiency while maintaining low carbon monoxide and nitrogen oxide emissions and allows continuous monitoring of boiler performance.
Combustion air and flue gas damper drives fill a critical role requiring safety, accuracy and reliability of the combustion control system. The proper damper drive delivers quality, power and performance providing precise control and speed increases the BTU/Fuel ratio and increases the MW/Fuel ratio.
Rotork offers a full-line of electric and pneumatic damper control solutions for the isolation and control of combustion air and flue gas. Our products improve the efficiency and reliability of large and small boilers, furnaces and process heaters.
DOWNLOAD THE ROTORK TYPE-K DAMPER DRIVE CATALOG FROM THIS WEB PAGE
For more information, contact Power Specialties, Inc. Call them at (816) 353-6550 or visit their web site at https://www.powerspecialties.com.
Top Five Tips for Choosing a Flow Meter
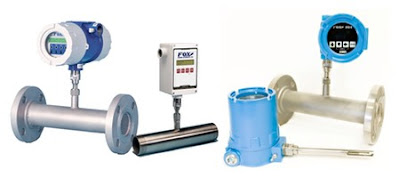
- Regulations, compliance
- What local, state, regional or national regulations impact the measurement location?
- Are there additional recording, data logging or calibration verification requirements to comply with regulations?
- What agency approvals must the flow meter have?
- Fluid type at the measurement point
- Dry or wet gas conditions may affect sensors
- Corrosive components in oil may affect sensor material selections
- Flow back contains mixtures of oil, gas, solids, chemicals, and water that must be separated
- Fluid conditions
- Does the accuracy spec of the flow meter change based on the composition of the fluid type?
- Does the fluid composition change over time?
- What is the pressure and velocity in the pipe? Is it constant?
- Are there installation limitations (straight pipe runs, limited access to the pipe, tight spaces)?
- Additional equipment
- Does the flow meter require additional equipment or instrumentation to operate successfully at the point of measurement?
- Additional calculations
- Will you need to do additional calculations to determine an accurate flow rate?
List is courtesy of Fox Thermal.
Power Specialties, Inc.
9118 E. 72nd Terrace
Raytown, MO 64133
Toll Free: (800) 432-6550
Phone: (816) 353-6550
Fax: (816) 353-1740
www.powerspecialties.com
Top 10 Reasons Why ProSafe-RS Safety Instrumented System (SIS) Is the Fastest Growing Safety Control System
Before ProSafe-RS, DCSs and SISs were typically supplied by different vendors and required extra engineering for the individual systems and interconnections. Furthermore, these systems were more difficult to master and operate as they had different interfaces. ProSafe-RS overcomes these hurdles through complete integration with Yokogawa’s CENTUM DCS – an industry first. The ProSafe-RS has been a global success since its debut in 2005, and is continually being improved.
ProSafe-RS has a unique and excellent dual architecture that is based on Yokogawa’s supremely reliable DCS technology. The SIS has a modular design, and dual architecture is implemented inside each module. And the modules themselves can be installed in a dual redundant configuration. This is controlled by the SIS and is fully transparent to the user. This approach maximizes both safety and availability, independently and simultaneously. This flexible system configuration makes it possible for the user to configure redundancy on a module by module basis, achieving the required availability in each system component.
For more information about Yokogawa's ProSafe-RS, contact Power Specialties, Inc. Call them at (816) 353-6550 or visit their web site at https://powerspecialties.com.
A Better Solution for Open Channel Flow Measurement
Open channel flow instruments require accurate measurement of the surface level of a liquid. A flume, channel or structure which has a known characteristic flow per measured head, together with the measured liquid level, accurately define the flow rate through the system.
Traditional systems use a stilling well and pressure level measurement system to measure the liquid level in the structure. Sedimentation and buildup will over time cover the sensing part of a pressure measurement system, leading to inaccurate or completely failed measurement. Buildup can also block passages to a stilling well, making any level measurement inaccurate or false. Regular cleaning of measurement systems and stilling wells is required to ensure operation.
The level instrumentation control manufacturer Hawk Measurement uses a non-contact Acoustic Wave sensor, positioned directly over the channel or flow structure, or above the stilling well if required, to provide maintenance free, reliable measurement of the liquid level.
The Hawk Sultan Flow instrument calculates flow through a range of standard measurement structures, and can also be individually tailored to a non-standard flow characteristic. Measurements are temperature compensated, and sensors are available covering a broad range of water, waste-water, irrigation and environmental monitoring applications.
Powerful measurement pulses keep sensor facings clean from moisture and condensation, ensuring maximum performance in all conditions. Continuous and switched outputs are included, as well as local totalizing of flow, and the ability to provide pulsing outputs per flow volume to external counting devices.
For more information, contact Power Specialties, Inc. Call them at (816) 353-6550 of visit their site at https://powerspecialties.com.
![]() |
Hawk transducer for water applications. |



For more information, contact Power Specialties, Inc. Call them at (816) 353-6550 of visit their site at https://powerspecialties.com.
Labels:
flow measurement,
flow sensor,
Hawk,
Iowa,
Kansas,
level sensor,
Missouri,
Nebraska,
open channel
US Power Grids, Oil and Gas Industries, and Risk of Hacking
A report released in June, from the security firm Dragos, describes a worrisome development by a hacker group named, “Xenotime” and at least two dangerous oil and gas intrusions and ongoing reconnaissance on United States power grids.
Multiple ICS (Industrial Control Sectors) sectors now face the XENOTIME threat; this means individual verticals – such as oil and gas, manufacturing, or electric – cannot ignore threats to other ICS entities because they are not specifically targeted.
The Dragos researchers have termed this threat proliferation as the world’s most dangerous cyberthreat since an event in 2017 where Xenotime had caused a serious operational outage at a crucial site in the Middle East.
The fact that concerns cybersecurity experts the most is that this hacking attack was a malware that chose to target the facility safety processes (SIS – safety instrumentation system).
For example, when temperatures in a reactor increase to an unsafe level, an SIS will automatically start a cooling process or immediately close a valve to prevent a safety accident. The SIS safety stems are both hardware and software that combine to protect facilities from life threatening accidents.
At this point, no one is sure who is behind Xenotime. Russia has been connected to one of the critical infrastructure attacks in the Ukraine. That attack was viewed to be the first hacker related power grid outage.
This is a “Cause for Concern” post that was published by Dragos on June 14, 2019.
“While none of the electric utility targeting events has resulted in a known, successful intrusion into victim organizations to date, the persistent attempts, and expansion in scope is cause for definite concern. XENOTIME has successfully compromised several oil and gas environments which demonstrates its ability to do so in other verticals. Specifically, XENOTIME remains one of only four threats (along with ELECTRUM, Sandworm, and the entities responsible for Stuxnet) to execute a deliberate disruptive or destructive attack.
XENOTIME is the only known entity to specifically target safety instrumented systems (SIS) for disruptive or destructive purposes. Electric utility environments are significantly different from oil and gas operations in several aspects, but electric operations still have safety and protection equipment that could be targeted with similar tradecraft. XENOTIME expressing consistent, direct interest in electric utility operations is a cause for deep concern given this adversary’s willingness to compromise process safety – and thus integrity – to fulfill its mission.
XENOTIME’s expansion to another industry vertical is emblematic of an increasingly hostile industrial threat landscape. Most observed XENOTIME activity focuses on initial information gathering and access operations necessary for follow-on ICS intrusion operations. As seen in long-running state-sponsored intrusions into US, UK, and other electric infrastructure, entities are increasingly interested in the fundamentals of ICS operations and displaying all the hallmarks associated with information and access acquisition necessary to conduct future attacks. While Dragos sees no evidence at this time indicating that XENOTIME (or any other activity group, such as ELECTRUM or ALLANITE) is capable of executing a prolonged disruptive or destructive event on electric utility operations, observed activity strongly signals adversary interest in meeting the prerequisites for doing so.”
Creating a Calibration Curve with the CHINO IMRA Infrared Multi Analyzer
The CHINO IMRA on-line multi IR wavelength analyzer utilizes infrared absorption technology to measure moisture, film-thickness, organic properties, and coating-thickness in real time. Signal processing capabilities are built into the compact, stand-alone detector unit for easy installation and operation. A maximum of 99 calibration curves can be stored into the detector memory for numerous measurement applications. This video demonstrates how to create a calibration curve. In this demonstration, moisture content is measured in sand.
For more information about CHINO moisture, film-thickness, organic properties, and coating-thickness analyzers, contact Power Specialties, Inc. by calling (816) 353-6550 of visit their website at https://powerspecialties.com.
Labels:
Chino,
coating thickness,
film-thickness,
Iowa,
IRMA,
Kansas,
Missouri,
Moisture detection,
Nebraska,
organic properties
Rotameters a.k.a Variable Area Flow Meters
![]() |
Rotameter (Yokogawa) |
Rotameters have diverse industrial processing applications that range from simple to sophisticated. The devices are easy to install, require no electrical connection, and provide direct flow rate reading. They provide fail-safe flow rate in different situations.
The post will highlight the workings of rotameters, also known as a variable area flow meter.
Rotameters: An Overview
Invented by German inventor Karl Kueppers in 1908, rotameters measure the volumetric flow rate of liquids and gases. The device was so named because it functions by rotating in a tube.
Important elements of a rotameter include the tube and the float.
The tube is fixed vertically and liquid is fed from the bottom. The fluid is fed from the bottom that travels upward and exits from the top. The float remains at the bottom when no liquid is present and rises upward when fluid enters the tube.
The float inside the tube moves in proportion to the rate of fluid flow and the area between the tube wall and the float. When the float moves upward, the area increases while the differential pressure decreases. A stable position is reached when the upward force exerted by the fluid is equal to the weight of the float. A scale mounted on the tube records the flow rate of the liquid.
Every float position shows a specific flow rate for the viscosity and density of a liquid. The device helps in determining the flow rate by matching the position of the float to a scale on the rotameter. The flow can be adjusted manually using a built-in valve.
Types of Rotameters
Rotameters can be categorized by the type of tube. A sharp metering edge is located on the float from where the reading is observed by a scale on the tube. The connections and end fittings of the various types of rotameters are different.
Glass Rotameter
![]() |
Glass rotameters (Yokogawa) |
The basic glass rotameters consist of borosilicate glass tube while the float is made of either glass, plastic, or stainless steel. The most common combination is a glass tube and metal float. This is suitable for a measure the flow rate of liquid of low to medium temperature and pressure.
Flow rate is determined by the spring and piston combination of the rotameter. The materials and fittings should be chosen as per the temperature and pressure of the liquid.
Metal Rotameter
Metal tube rotameters are another type that is suitable for temperatures and pressures beyond the glass tubes. They are generally manufactured of stainless steel, aluminum, and brass. The piston position is determined by the mechanical and magnetic followers that can be read from the outside of
the tube.
the tube.
![]() |
Metal rotameter (Yokogawa) |
Industrial Applications of Rotameters
The use of rotameter extends across different industries. The device is extensively used in industries since its an economical way to measure a range of flow rates in almost any conditions.
Sample Process Analysis
Rotameters are widely used in sample process analysis. A device with 4 to 20 mA output is used to measure the flow of a sample system. Monitoring the flow rate ensures that the system does not become plugged that could result in big problems. The device can indicate when the flow starts to drop so that the maintenance crew can address the problem before it results in major damage.
Transport of Liquid Natural Gas
LNG must be re-gasified during transport to prevent system overpressure that could cause major damage to the storage system. Rotameter can measure the flow rate of vented vapor even at very low temperature. They are ideal for determining the LNG flow rate during transport due to being low cost and providing an accurate reading.
Rotating Equipment
Rotameters are also used in measuring the flow of liquid in large rotating equipment. They are used to measure the flow rate of dry gas, coolants, lubricant fluids to ensure safe operations. The device helps in monitoring of coolant flows a lube oil. The flow can be measured continuously due to the use of 4— 20 mA transmitting rotameters.
Benefits of Rotameters
Rotameters, or variable area flow meters are cost-effective for use in different industrial applications. The price and low maintenance of the device contribute to significant savings for industrial concerns.
Another advantage of rotameters is that no external power is required. They are mechanical device and no external power source is required to measure the flow rate. This makes it possible for the device to be used in remote and hazardous areas where installing an external power supply can be costly.
The design of the rotameter allows not the only the measurement of fluid flow but also determine the quality of the liquid. The crew members can see whether the fluid is dirty thereby requiring a change of filter. They can also know whether bubbles are present in the liquid and also whether the liquid is of the correct color.
Rotameters can be installed along with other flow measuring devices to ensure accurate readings. The device can continuously determine an accurate flow rate. They are simple to install and easy to maintain. Just connect the process line to rotameter’s inlet and outlet pipe. That’s why they are commonly used in many industries where it’s critical to accurately measure the flow rate of the liquid.
Contact Power Specialties, Inc. with any questions regarding the use of rotameters. Call them them at (816) 353-6550 or visit https://powerspecialties.com.
Understanding the Operation of Coriolis Flow Meters
![]() |
Coriolis flow meter (Yokogawa ROTAMASS) |
Coriolis flow meters are used in a variety of industries ranging from oil and gas, petrochemicals, and food to chemical, life sciences, and — particularly — in transfer applications.
How Does a Coriolis Flow Meter Work?
Coriolis flow meters work on the principle of Coriolis Force that was first explained by a French engineer and mathematician Gaspard-Gustave de Coriolis in the 19th century. The Coriolis force represents an inertial force that acts on bodies in a rotating frame of reference.
Also known as inertial mass flow meters, Coriolis flow meters measure fluid flow through inertia. The device has one or more measuring tubes that vibrate due to the force produced by an actuator. The twisting force inside the measuring tube is directly proportional to the mass flow of the liquid.
![]() |
Measurement Principle of the Coriolis Flow Meter (1) (courtesy of Yokogawa) |
The sine waves are in phase with each other when there is no liquid flow. Once the liquid flows through the tube, the measuring tubes twist depending on the mass flow. The sensors detect the extent of the twist by assessing the phase shift in the sine waves. The difference in phase shift helps in determining the mass flow rate.
Volumetric flow is determined by dividing the mass flow rate by the density of the liquid.
Density change is determined by assessing the change in oscillation frequency in response to the excitation inside the tube. The higher the mass flow rate, the lower will be the frequency change and density of the liquid flow.
![]() |
Measurement Principle of the Coriolis Flow Meter (2) (courtesy of Yokogawa) |
Lastly, Coriolis flow meters can also be used to measure the temperature inside the tube. The device has sensors inside the tube that can detect temperatures of up to 752 F or 400 C.
The Pros and Cons of Coriolis Flow Meters
Coriolis flow meters can assess liquid flow in both forward and reverse directions. Advanced Coriolis meters have dual curved tubes that can measure with more accuracy. Moreover, the device with curved tubes is characterized by lower pressure drop, making them ideal in specific situations such as wastewater handling, chemical processing, pulp and paper processing, and oil and gas industries.
Another application of Coriolis flow meters is in the pharmaceuticals and food and beverage industries. They can be used with a straight tube design so they are easy to clean. The flow meters are also used in scientific studies for measuring corrosion and assessing liquids and gases. In addition, the flow meters are used in mining operations to monitor liquid flow rate.
While Coriolis meters allow accurate assessment of fluid flow, they are not free from errors. The device can show inaccurate reading when air bubbles are present. The bubbles create splashing that results in generate inaccurate readings. They change the energy required for tube oscillation, resulting in a false assessment of fluid flow.
A lot of energy is spent in the vibration of the tube, especially in case of large spaces. This can also result in failure of accurate assessment of liquid flow inside the tube.
Installation and Calibration of Coriolis Flow Meter
Coriolis flow meter must be installed with full liquid so that no air gets trapped inside the tube. The meter should also be drained completely before use. The ideal location for the flow meter is a vertical pipe mount with an upward flow of fluid.
The Reynolds number is not a limitation with the Coriolis meter. In addition, there is no need for accounting for swirl and velocity profile distortion. As a result, the device can be used without adjusting for straight runs of relaxation piping to condition the liquid flow.
An air release upstream of the meter should be installed if there is a likelihood of air bubbles. In addition, filters, strainers, or air/vapor eliminators can help prevent air bubbles inside the tube. Control valves can also be installed to increase the back-pressure and reduce the likelihood of flashing.
For more information on Coriolis flow meters contact Power Specialties by calling (816) 353-6550 or by visiting https://powerspecialties.com.
Industrial Air Flow Measurement Products

This catalog includes solutions for:
- COMBUSTION AIRFLOW APPLICATIONS
- Power, Biomass, and Recovery Boilers
- Heaters, Furnaces, Ovens, and Kilns
- CLEAN AIR PROCESS APPLICATIONS
- Aeration to Digesters
- DIRTY AIR PROCESS APPLICATIONS
- Dust Collection Systems
- Quench Exhaust
- PRESSURE MEASUREMENT
- Clean room Pressurization
For more information, contact:
Power Specialties, Inc
(816) 353-6550
How to Select and Use the Right Temperature Sensor

Courtesy of Pyromation and Power Specialties, Inc.
Yokogawa SENCOM 4.0 Platform: The Next Generation in Liquid Analyzers
SENCOM™ 4.0 Platform technology allows pH and ORP sensors to transmit and receive data when connected to FLXA402 analyzer or to any PC/tablet with Mobile Field Device Management (FieldMate) installed.
Designed with a strong focus on Yokogawa’s digital SMART sensors, the SENCOM SMART Sensor Platform provides greater insight and enhanced capabilities to deliver more credible data throughout the entire product lifecycle.
Yokogawa’s SENCOM SMART Sensor Platform is an innovative analyzer platform that optimizes maintenance, reduces configuration time, and simplifies in-field maintenance and calibration.
For more information, contact Power Specialties, Inc.
https://powespecialties.com
(816) 353-6550
Level Measurement White Paper

Repeatable and Reliable Level Measurement for Granular Activated Carbon in Corn Syrup Production
Granular activated carbons (GAC) are prepared from a variety of local raw materials of vegetable origin such as wood and peat, or of mineral origin, such as coal.
The presence of suspended particles in the production of corn syrups impacts the efficiency of steps in the refining process. These suspended particles are removed during clarification using granular activated carbon (GAC). GAC is used for both decolorization and to filter impurities such as amino acids and polysaccharides.
A corn syrup producer was looking for a reliable, low maintenance level transmitter to measure GAC in a carbon column.
It is important to measure the granular activated carbon level because, after the GAC filters out the impurities, the spent GAC is then mixed and cleaned with water forming a slurry, which is pumped into carbon columns. The level of the granular activated carbon slurry in the column must be accurately measured so it can be separated from the water and conveyed back to the reactivation furnace. The level inside the column is critical to the efficiency of the re-carbonizing process.
Other technologies, including the electromechanical displacer level systems, had been tried without success. The client wanted a reliable, low maintenance solution.
SOLUTION
The Hawk ORCA Sonar low frequency interface transmitter, with automatic sludge cleaning, was installed and tested. The ORCA's low frequency sonar was able to measure the GAC interface very accurately through the dirty, sticky and viscous black water. The ORCA system provided high reliability and excellent repeatability, which improved automation control and reduced maintenance downtime.
The ORCA Sonar Bed Level transducer emits a high powered acoustic pulse, which is reflected from the interface density selected. The reflected signal is processed using specially developed software algorithms, that eliminate lighter floating densities and stratified layers, allowing measurement of RAS or BED levels. It can be calibrated to measure lighter densities like FLOC or one of the outputs could be used for a CLARITY output, similar to a basic turbidity transmitter measuring solids in suspension. By choosing the correct sonar transducer frequency, the ORCA sonar guarantees the optimized performance when measuring both light and heavy density interfaces.
For more information, contact Power Specialties, Inc. Call them at (816) 353-6550 or visit their web site at https://powerspecialties.com.
The presence of suspended particles in the production of corn syrups impacts the efficiency of steps in the refining process. These suspended particles are removed during clarification using granular activated carbon (GAC). GAC is used for both decolorization and to filter impurities such as amino acids and polysaccharides.
A corn syrup producer was looking for a reliable, low maintenance level transmitter to measure GAC in a carbon column.
It is important to measure the granular activated carbon level because, after the GAC filters out the impurities, the spent GAC is then mixed and cleaned with water forming a slurry, which is pumped into carbon columns. The level of the granular activated carbon slurry in the column must be accurately measured so it can be separated from the water and conveyed back to the reactivation furnace. The level inside the column is critical to the efficiency of the re-carbonizing process.
Other technologies, including the electromechanical displacer level systems, had been tried without success. The client wanted a reliable, low maintenance solution.
SOLUTION
The Hawk ORCA Sonar low frequency interface transmitter, with automatic sludge cleaning, was installed and tested. The ORCA's low frequency sonar was able to measure the GAC interface very accurately through the dirty, sticky and viscous black water. The ORCA system provided high reliability and excellent repeatability, which improved automation control and reduced maintenance downtime.
The ORCA Sonar Bed Level transducer emits a high powered acoustic pulse, which is reflected from the interface density selected. The reflected signal is processed using specially developed software algorithms, that eliminate lighter floating densities and stratified layers, allowing measurement of RAS or BED levels. It can be calibrated to measure lighter densities like FLOC or one of the outputs could be used for a CLARITY output, similar to a basic turbidity transmitter measuring solids in suspension. By choosing the correct sonar transducer frequency, the ORCA sonar guarantees the optimized performance when measuring both light and heavy density interfaces.
For more information, contact Power Specialties, Inc. Call them at (816) 353-6550 or visit their web site at https://powerspecialties.com.
Labels:
Corn Syrup,
Granular Activated Carbon,
Hawk Measurement,
Iowa,
Kansas,
Level,
Missouri,
Nebraska,
Sonar
The Yokogawa YS1700 Replaces the Obsolete Siemens/Moore 353 Controller
Now that entire Moore/Siemens 350 family is obsolete, are you considering upgrading to a DCS?
Are you concerned about the cost and time for a new installation, application development and personnel training?Is it possible that the new equipment vendor may again leave you stranded with their equipment as their core business is not industrial automation and control?
We have a better solution for you: Yokogawa and its YS1700 PID loop controller. Yokogawa has been providing industrial solutions, as their primary business, for over a century and their YS1700 will keep you off of eBay looking for spare 353 parts.
Pyromation: The Premier Manufacturer of RTD Temperature Sensors, Thermocouples & Thermowells In North America
Pyromation is one of the leading manufacturers of thermocouples, RTDs, PT100s and thermowells in North America. As an ISO 9001-registered company, Advanced Manufacturing Firm and Lean enterprise with an onsite NVLAP-Accredited Metrology Laboratory (Lab Code 200502-0), the Fort Wayne, IN-based operation's team members are invested in providing the best solution for each customer's application. Pyromation produces a variety of temperature sensors and assemblies in both standard and custom designs, which can be found on equipment and in process applications in the chemical, petrochemical, power generation, food & beverage, dairy, plastics, heat-treating, oil & gas, pharmaceutical, aerospace, biomass, metal processing, rubber, mining, HVAC, water & wastewater, incineration and many other industries in North America and around the world.
This video provides a short introduction to their capabilities, plant, and people.
Power Specialties, Inc.
https://powerspecialties.com
(816) 353-6550
Case Study on Thermal Flow Meter Calibration for Natural Gas Service
A study of the importance of gas composition and calibration and their effects on flow meter accuracy.
Errors associated with the calibration of flow meters for natural gas service can be costly but can also be mitigated using an advanced flow meter design that allows field-adjustment of the natural gas composition without loss of accuracy.Or, read the embedded document below. For more information, contact Power Specialties, Inc. by calling (816) 353-6550 or visit https://powerspecialties.com.
For Over 50 Years Customers Have Trusted Power Specialties
Established in 1967, Power Specialties was founded on the concept that customer service is of primary importance. Our staff of Sales Engineers are well trained in the application and selection of instrumentation and control products. Call us with your next process instrumentation, process weighing, or process equipment requirement.
Power Specialties, Inc.
https://powerspecialties.com
(816) 353-6550
White Paper: Six Fixed Gas Detection Innovations to Consider for Safer Facilities
This white paper, courtesy of MSA, details the how the latest digital technologies and advances in materials and construction techniques are improving fixed gas detectors for more efficient plant safety. Topics include electrochemical cell sensor advances, laser-based gas open path detectors, onboard diagnostics-ease of maintenance, wireless Bluetooth, data and communications and dual gas sensor transmitters.
Download the "Six Fixed Gas Detection Innovations to Consider for Safer Facilities" from this link.
Download the "Six Fixed Gas Detection Innovations to Consider for Safer Facilities" from this link.
SMART Liquid Analyzer Communications System with Yokogawa SENCOM™

Digital or SMART sensors maintain specific measurement and calibration data on an integrated chip along that is an integral part of the sensor. This data can be exchanged between the sensor and either a process transmitter or a laboratory PC using a data management software, like the SPS24.
For more information, contact Power Specialties by calling (816) 353-6550 of visit https://powerspecialties.com.
Subscribe to:
Posts (Atom)